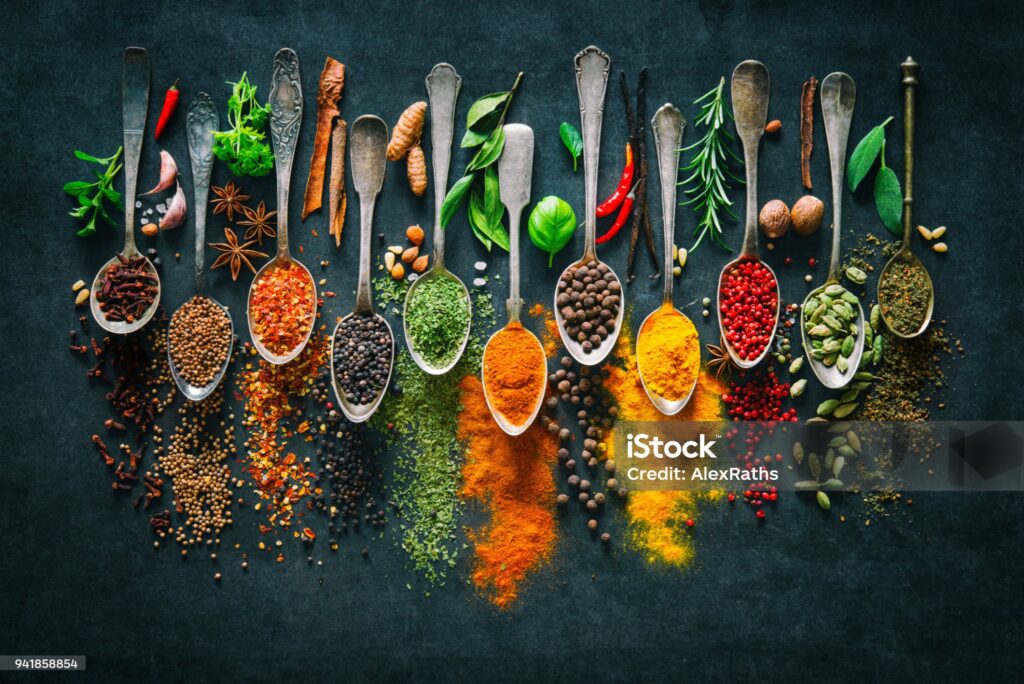
Understanding the economic landscape of freeze-dried food products begins with recognizing the various cost components involved in the freeze drying process, namely equipment, energy, and labor. Each plays a pivotal role in the overall costing framework and impacts the efficiency of production.
Cost Components in Freeze Drying
Freeze drying equipment embodies a significant capital investment, with advanced machines featuring vacuum systems and large drying chambers. Dependable energy consumption during the sublimation phase drives utility bills higher, while skilled labor is necessary to manage the nuanced freeze drying process to ensure superior product quality.
Balancing the interplay between product excellence and production expenditures presents a strategic challenge. Producers strive to maintain high-quality outputs without inflating costs, a balance that determines market competitiveness.
Market Pricing and Return on Investment
Freeze-dried foods retain a higher market value rooted in their extended shelf life and preserved nutrition. Manufacturers price these products to reflect the sophisticated processing, setting a premium over conventional drying methods. This pricing strategy is pivotal to realizing a favorable return on investment. Substantial initial costs associated with freeze drying technology necessitate informed pricing models to assure profitability in the long term.
- Equipment expenditures relate directly to the scale of operations, with larger systems garnering higher outputs but also incurring greater costs.
- Energy expenses fluctuate with regional costs and efficiency measures; the optimization of the freeze drying cycle can result in substantial savings.
- Labor costs vary based on expertise required, with specialized training contributing to successful operations.
The freeze drying process, therefore, must be scrutinized in light of these economic factors. Companies must analyze the interdependencies of cost, quality, and throughput to optimize their return on investment and secure a stronghold within the industry.